Système de lavage de film PP PE : Augmenter les profits et l'efficacité du recyclage
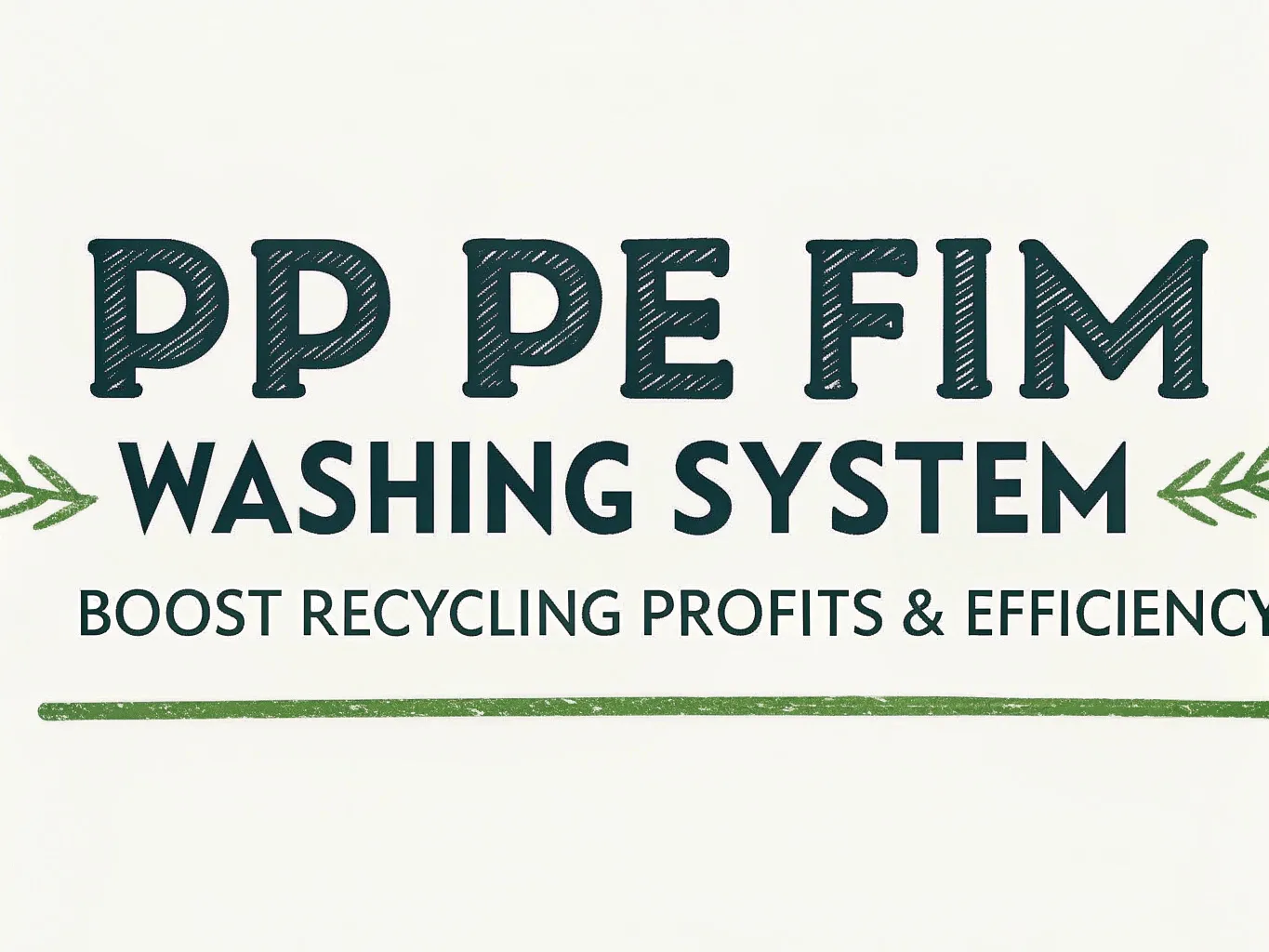
La tendance mondiale en faveur du développement durable et de l'économie circulaire a placé le recyclage du plastique au cœur des préoccupations. Les films en polypropylène (PP) et en polyéthylène (PE), couramment utilisés dans...