O guia definitivo das linhas de lavagem para reciclagem de garrafas PET
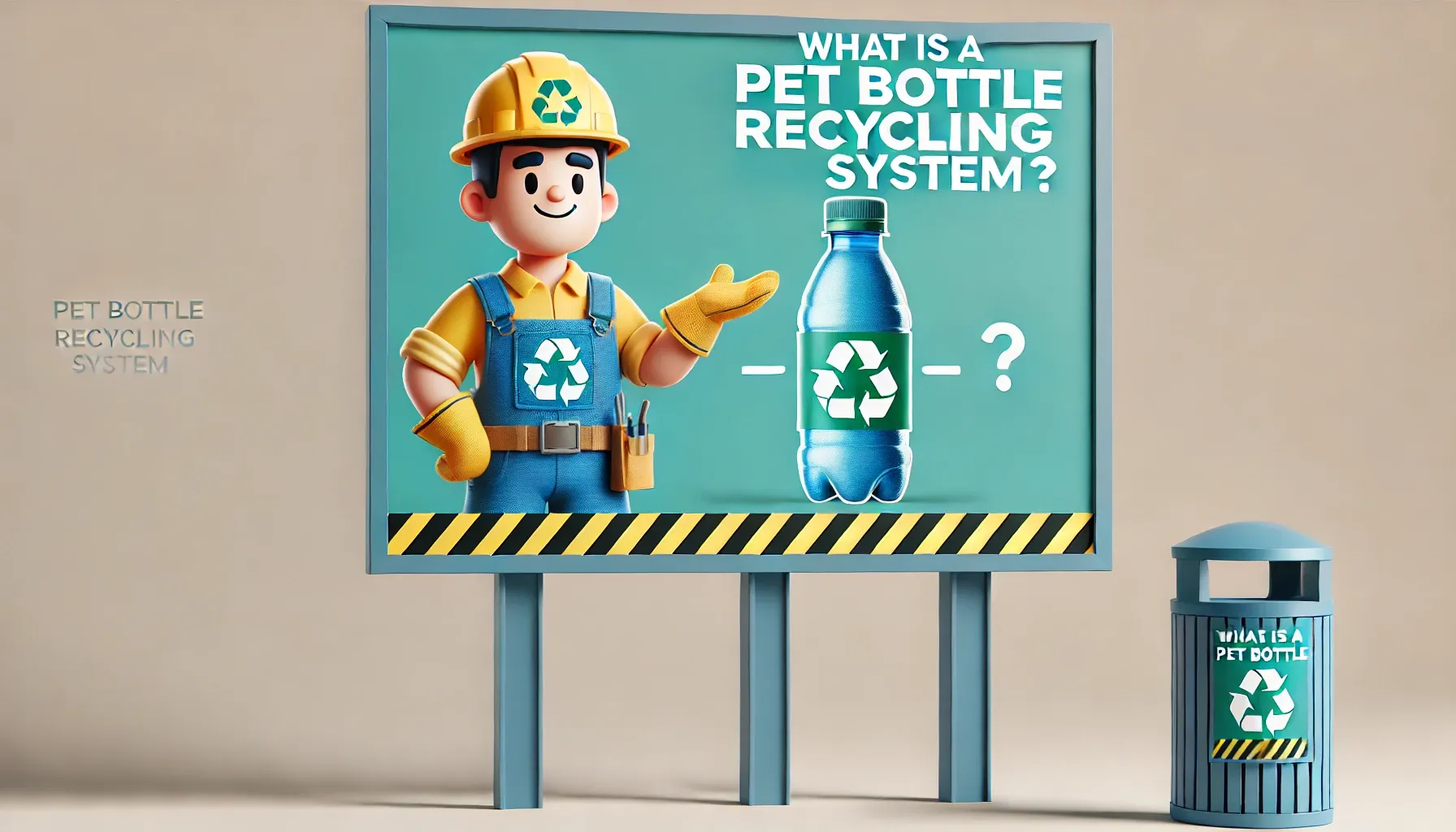
Uma linha de lavagem para reciclagem de garrafas PET é um sistema avançado e integrado de máquinas concebidas com um objetivo principal: transformar garrafas PET pós-consumo altamente contaminadas e enfardadas...