Turnkey Recycling Systems for Rigid PE & PP Plastics
A fully integrated, turnkey solution engineered for the reclamation of post-consumer and post-industrial rigid plastics. This system transforms contaminated PE/PP material streams into high-purity, production-ready recycled flakes, meeting the stringent demands of today’s circular economy.
Request a Customised QuoteWhy Choose Our Recycling Line?
Our systems deliver tangible economic and environmental returns through superior engineering and tailored design.
High-Purity Output
Our multi-stage process ensures flakes with >99% purity and <1% moisture, increasing the value of your final product and unlocking new market opportunities.
Customised Solutions
We don’t offer one-size-fits-all. Each line is engineered to handle your specific feedstock and contamination levels, maximizing throughput and efficiency.
Robust & Efficient
Built with high-wear resistant components and designed for operational efficiency, our lines minimize downtime and reduce your operational costs for a faster ROI.
From Waste to Raw Material
Our automated system transforms contaminated rigid plastics into a valuable commodity through a clear, efficient process.
1. Size Reduction
Shredding & Granulation
2. Washing
Friction & Float-Sink
3. Drying
Centrifugal & Thermal
4. Purification
Air Classification
Detailed Process Overview:
- Infeed & Pre-Shredding: Baled or loose feedstock is fed into a heavy-duty shredder for initial size reduction.
- Granulation & Initial Wash: The material is conveyed to a wet granulator, which creates uniform flakes while performing a preliminary wash.
- High-Friction Washing & Density Separation: Intensive scrubbing removes stubborn dirt, followed by sink-float separation to eliminate high-density contaminants.
- Mechanical & Thermal Dewatering: A high-speed centrifugal dryer removes bulk water, then a thermal system achieves a final moisture content of <1%.
- Fines & Label Separation: An air-based Zig-Zag classifier removes light-fraction contaminants like paper labels and dust.
- Automated Bagging: The final, purified plastic flakes are automatically dispensed into storage bags.
Our Equipment in Action
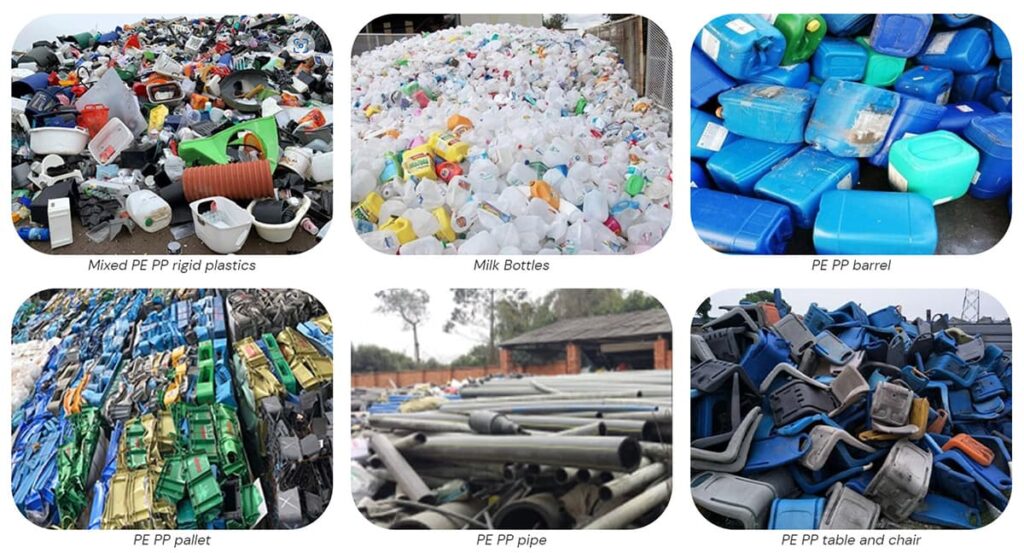
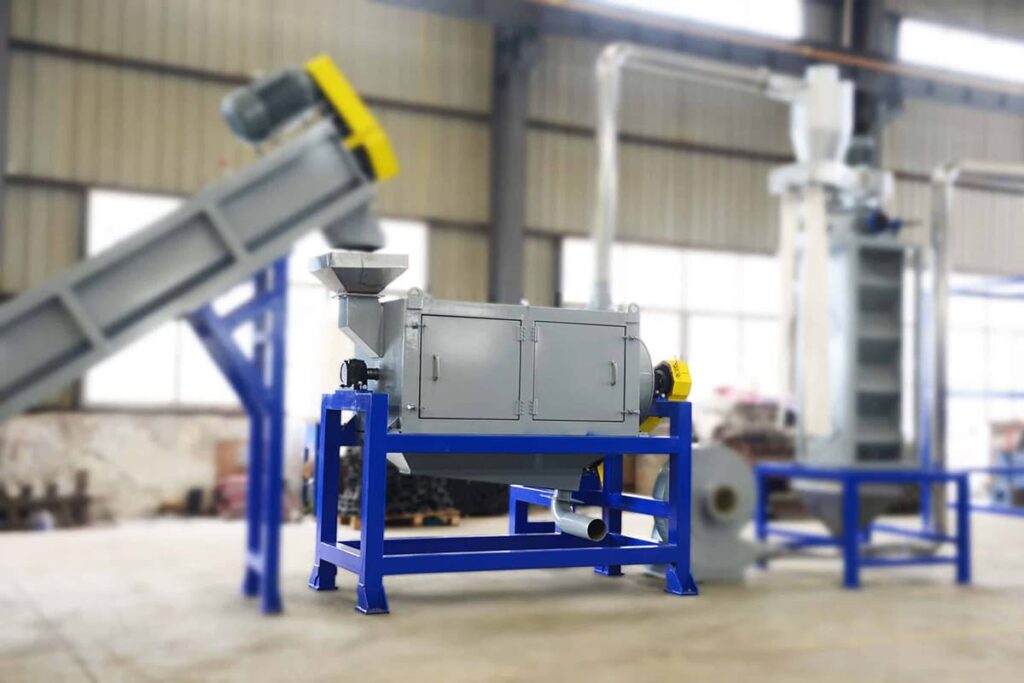
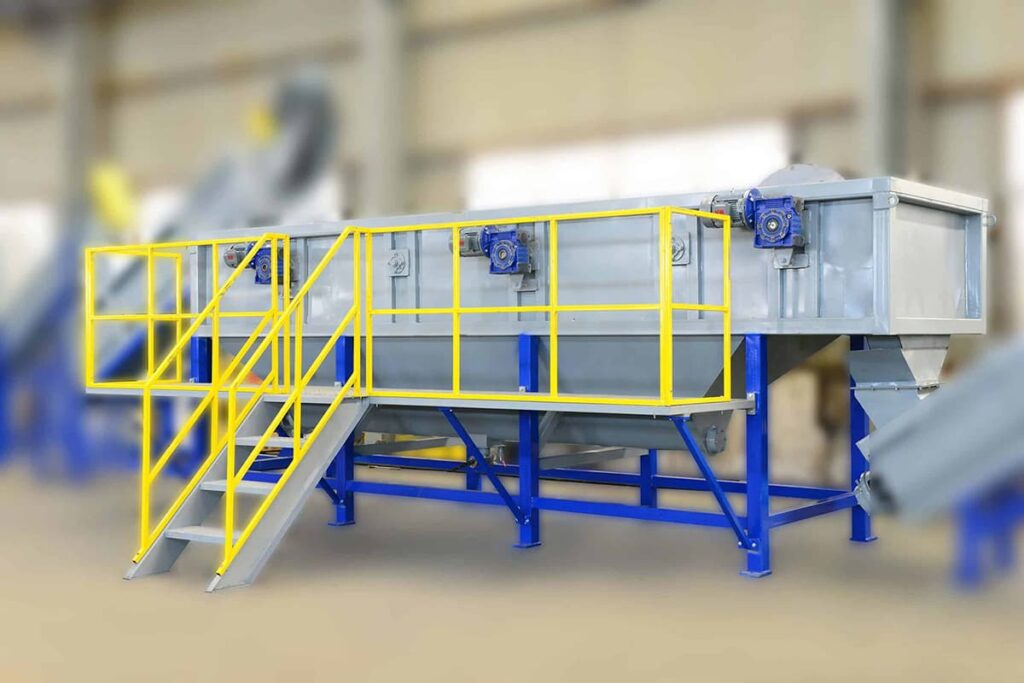
System Components & Specifications
Sprzęt | Core Function & Technical Benefit |
---|---|
Feeding Conveyor | Provides a consistent, uniform material feed rate, which is critical for the stable and efficient operation of the entire line. |
Niszczarka | High-torque, low-speed shredding of bulky materials to protect downstream equipment and prepare a homogenous input for the granulator. |
Granulator | Performs wet granulation, reducing particle size to a specified dimension while initiating the washing process to improve overall cleaning efficiency. |
Sink-Float Tank | Utilizes water density to separate target polyolefins (PE/PP) from heavier contaminants (metals, rocks) and other plastics (PET, PVC). |
Suszarka odśrodkowa | A high-speed mechanical dewatering unit that rapidly removes the majority of surface moisture, significantly reducing the load on the thermal dryer. |
System suszenia termicznego | Employs hot air circulation to achieve a final moisture content below 1%, ensuring the flakes are production-ready for high-quality extrusion. |
Klasyfikator zygzakowaty | A final air-based purification step that precisely removes light-fraction contaminants like paper labels, film, and dust. |
Główne parametry techniczne
Pojemność wejściowa | 500kg/godz. | 1000kg/godz. | 1500kg/godz. | 2000kg/godz. |
---|---|---|---|---|
Wymagana przestrzeń | 42m×10m×6m | 50m×15m×6m | 55m×16m×6m | 60m×18m×6m |
Operatorzy | 3-4 osoby | 5-6 osób | 5-6 osób | 5-6 osób |
Moc instalacji | 150-200kW | 250-300kW | 370kW | 450-500kW |
Cyrkulacja wody (T/H) | 2 | 3 | 4 | 5 |
Note: The table outlines standard models. We specialize in customizing lines based on feedstock analysis and desired throughput.
Często zadawane pytania
1. What is the typical lead time from order to delivery?
Standard configuration lines typically have a lead time of 60-90 days. For fully customized systems, the lead time will be determined after a detailed technical consultation and provided with your formal quotation.
2. Do you provide installation and training services?
Yes, we offer comprehensive support. Our service packages include on-site installation supervision, system commissioning, and operational training for your staff to ensure a smooth startup and efficient, safe operation.
3. What are the utility requirements for the line (power, water)?
Utility requirements vary by system capacity. A detailed list, including power consumption (kW) and water consumption rate (m³/hour), will be provided as part of our technical proposal for your chosen configuration.
4. How pure is the final recycled plastic flake?
Our systems are engineered for high-purity output, typically achieving >99% purity with a moisture content of <1%. The exact quality depends on the initial contamination level of the feedstock.
5. Are spare parts readily available?
Yes. We provide a detailed recommended spare parts list with every machine. Critical wear parts, such as shredder blades and granulator screens, are kept in stock for immediate dispatch to minimize any potential downtime.
6. Can the system be customized for my specific plastic waste?
Absolutely. Customization is one of our core strengths. We can modify components and adjust the process flow to optimize the line for your unique feedstock, whether it’s heavily soiled agricultural plastics or industrial scraps.
Request a Customized Proposal
Our engineering team is ready to analyze your specific requirements. Contact us for a technical consultation, detailed pricing, and lead time information.
All our recycling machines come with a 1-year limited warranty.