Panoramica del mercato delle macchine per il riciclaggio del PET nel 2025: tendenze di crescita e fattori trainanti
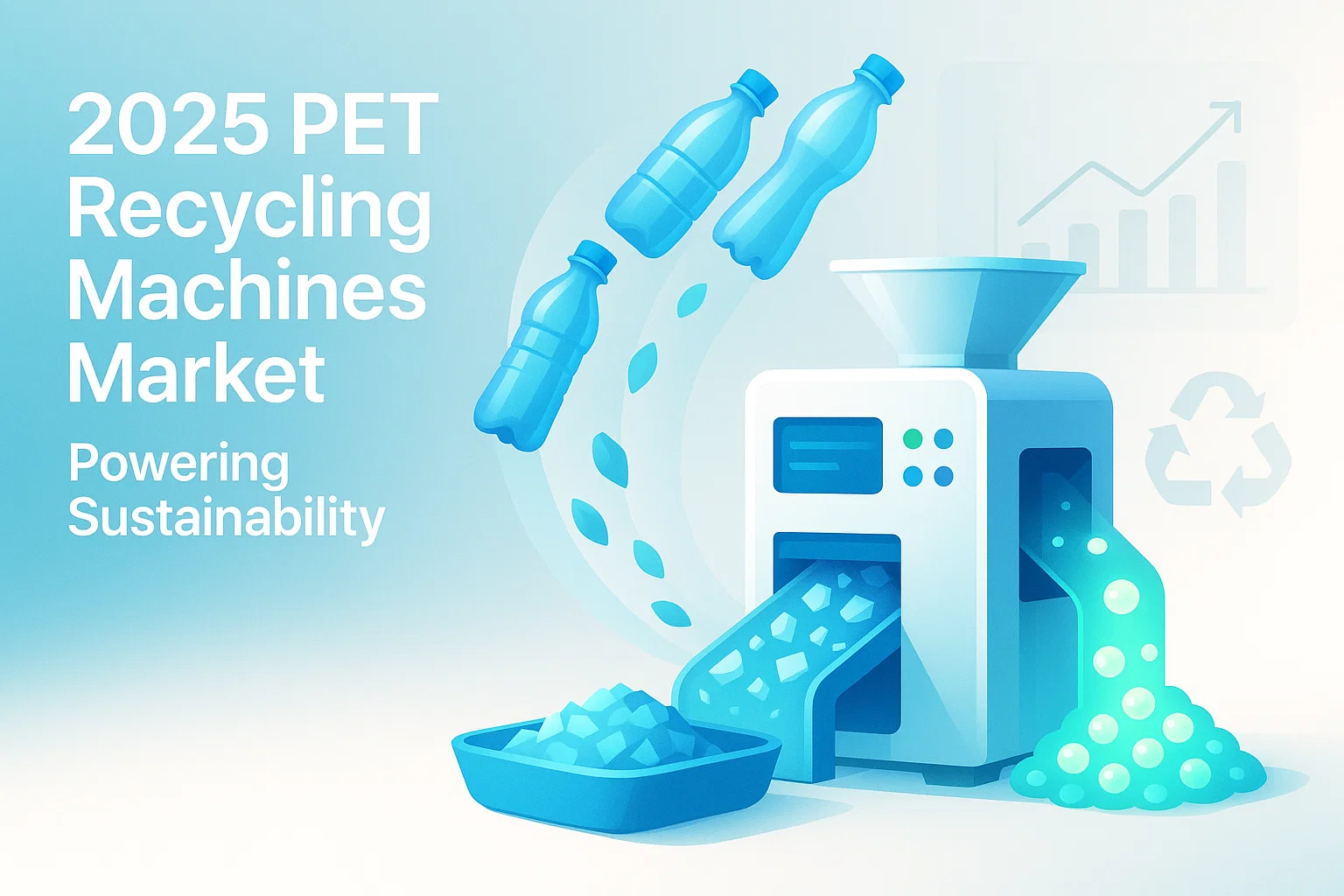
Con l'intensificarsi della spinta globale verso la sostenibilità, il mercato delle macchine per il riciclaggio del PET è destinato a una crescita significativa nel 2025 e oltre. Il polietilene tereftalato (PET), ampiamente utilizzato...