Sistema di lavaggio dei film in PP PE: Aumenta i profitti e l'efficienza del riciclaggio
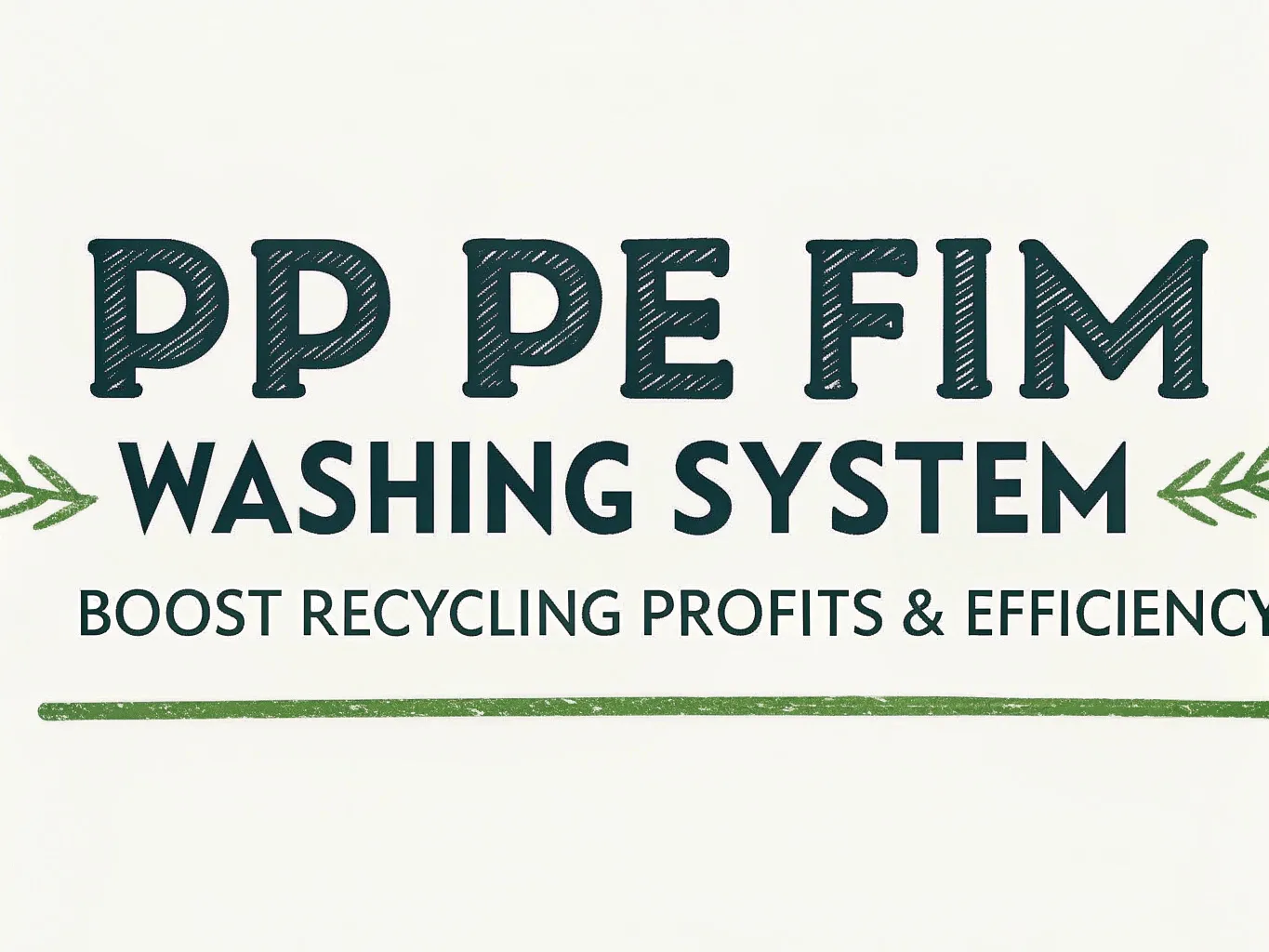
La spinta globale verso la sostenibilità e un'economia circolare ha posto il riciclo della plastica al centro dell'attenzione. Le pellicole in polipropilene (PP) e polietilene (PE), comunemente utilizzate in...