Discover Our Advanced PET Bottle Washing Line
Are you ready to kickstart or elevate your plastic bottle recycling business to new heights? Our comprehensive, state-of-the-art PET bottle washing line is your ultimate turnkey solution. This fully automated system efficiently transforms baled PET bottles into pristine, market-ready PET flakes, maximizing your operational efficiency and profitability.
Unlock Premium Value: High-Quality PET Flakes
With our meticulously engineered PET bottle washing line, you’re empowered to produce exceptionally high-quality PET flakes. These premium flakes command top dollar from manufacturers of polyester staple fiber and other high-value products. Furthermore, these flakes can be seamlessly pelletized into granules, opening diverse business opportunities in the production of various PET products.
Champion Sustainability: Environmental Benefits
Investing in our PET washing line is a significant step towards a greener planet. By recycling plastic bottles, you actively reduce landfill and ocean waste, conserve precious natural resources, and cut down on greenhouse gas emissions. Embrace this technology to become a key player in the circular economy, where materials are valued, reused, and repurposed rather than discarded.
Innovate with Confidence: Cutting-Edge Technology & Expertise
Backed by extensive global experience in PET bottle washing and recycling, we deliver not just machinery, but advanced recycling technologies and tailored technical solutions. Our profound expertise ensures you receive a robust system designed to adapt to the ever-evolving demands of the market and your valued customers.
A Strategic Investment for a Sustainable Future
Choosing our PET bottle washing line is more than an environmentally responsible decision—it’s a smart, profitable business move. Contact us today to explore how our complete PET bottle washing line can revolutionize your plastic bottle recycling operations and drive your success.
Main Technical Parameters
Input Capacity | 500kg/h | 1000kg/h | 1500kg/h | 2000kg/h | 3000kg/h |
---|---|---|---|---|---|
Required Space | 42m×10m×6m | 50m×15m×6m | 55m×16m×6m | 60m×18m×6m | 100m×20m×6m |
Operators | 3-5 people | 6-8 people | 7-9 people | 8-10 people | 10-12 people |
Installation Power | 150kW | 250kW | 370kW | 450kW | 750kW |
Water Circulation(T/H) | 2 | 3 | 3 | 4 | 5 |
“Post-consumer PET bottles are undoubtedly one of the most important components of the recycling market. Recycled PET can be used in a wide variety of applications and can bring significant financial returns to recycling companies.”
Core System Components: A Closer Look
Debaler Machine: The crucial first step in our plastic bottle washing line. This robust machine efficiently breaks the compacted bales of PET bottles, transforming them into a free-flowing stream ready for processing. Once “busted”, the bottles smoothly transition to the next stage.
Trommel (Optional): An effective optional component, the trommel is a slowly rotating cylindrical screen. Lined with precisely sized small holes (smaller than PET bottles), it allows for the removal of small contaminants like glass shards, metals, rocks, dirt, and paper, while PET bottles advance.
Wet Plastic Granulator: Often termed a plastic crusher, our high-performance granulator meticulously cuts PET bottles into uniform small flakes, typically between 10-15mm. With water constantly spraying into the cutting chamber, this wet granulation process not only sizes but also pre-treats and partially cleans the material.
Air Classifier: This intelligent system leverages air currents to separate lighter materials from heavier ones. Its primary function is to efficiently remove contaminants such as paper, cardboard, and loose plastic labels from the PET flakes, ensuring higher purity.
Sink/Float Separation Tank: Utilizing water’s density properties, this tank expertly separates materials. PET plastic, being denser, sinks, while lighter materials like plastic film (bottle labels) and PP/PE plastic (bottle caps) float. A screw conveyor at the tank’s bottom efficiently transports the valuable PET plastic to the next stage.
Hot Washer System: A critical stage for premium quality. Hot washing significantly enhances PET flake value by dissolving stubborn glues (from labels) and residues from leftover beverages/foods that are challenging to remove in cold wash processes. While water alone is effective, adding specialized washing agents can further optimize results.
Friction Washer: This high-efficiency cold water washing unit employs mechanical friction to vigorously scrub and remove any persistent dirt and debris from the PET flakes, ensuring a thoroughly cleaned product.
Dewatering Machine: The initial phase of the drying process. Our centrifugal dewatering machine utilizes high-speed centrifugal force to expel a significant portion of water from the PET flakes before they proceed to the thermal dryers, saving energy and time.
Thermal Dryer: PET flakes are pneumatically conveyed from the dewatering machine into the thermal dryer. Here, they travel through a series of stainless steel tubes, intermingling with hot air. This process ensures complete moisture removal via dehydration. An integrated cyclone separator then mixes the PET flakes with cool air, preparing them for storage.
Product Silo: A dedicated, hygienic storage tank for the clean, dry, and ready-to-market PET flakes.
Pelletizer/Extruder (Optional): While high-quality PET flakes are widely used as-is (especially in polyester fiber manufacturing), we also cater to clients requiring further processing. Our range includes advanced single-screw and twin-screw extruder pelletizers for converting flakes into pellets.
Detailed Process Flow
Step | Description |
---|---|
De-baling | Efficiently separating compacted PET bottles from bales into a manageable, free-flowing stream. |
Metal Removal | Strategically separating ferrous and non-ferrous metal materials using powerful magnets or advanced eddy current separators. |
Label Removal | Effectively removing labels from PET bottles through specialized chemical or mechanical processes to enhance flake purity. |
Metal Removal (Secondary) | A secondary stage for separating any residual metal materials, ensuring utmost purity of the PET stream. |
Bottle Pre-washing | Initial washing of the PET bottles to remove loose dirt and contaminants before the main washing process. |
Optical Bottle Sorting | Advanced sorting of PET bottles by type (e.g., PET, PVC) and color using high-precision optical sensors. |
Manual Sorting | Quality control stage involving further sorting of PET bottles by hand (by color, type, material, etc.) for specific requirements. |
Crushing (Granulation) | Shredding the PET bottles into consistently sized small pieces (flakes) for efficient cleaning and processing. |
Dust Removal | Removing fine dust particles from the shredded PET bottle pieces to improve downstream processing and final product quality. |
Flotation Hot Washing | Intensive cleaning of PET flakes using hot water (and optional detergents) in a flotation tank to remove glues, residues, and separate plastics by density. |
Friction Washing | Mechanical scrubbing to remove any remaining stubborn contaminants from the PET flakes using brushes or high-speed agitation. |
Rinsing | Thoroughly rinsing the cleaned PET flakes to remove any residual cleaning agents and fine particles. |
Flushing Washing | A final high-pressure water rinsing stage for the PET flakes to ensure maximum cleanliness. |
Drying | Efficiently drying the PET flakes using mechanical dewatering followed by thermal drying (hot air or spinning process) to achieve optimal moisture content. |
Dust Removal (Final) | Removing any remaining fine dust from the dried PET flakes for a pristine final product. |
Optical Flakes Sorting | Precision sorting of PET flakes by type (e.g. PET, PVC) and color using advanced optical sensors to meet specific quality standards. |
Blending | Homogenizing different colors and types of PET flakes to achieve consistent product characteristics as per customer requirements. |
Online Inspection | Continuously inspecting the quality of the PET flakes on the production line to ensure adherence to specifications. |
Packing | Securely packaging the final PET flakes in bags, super sacks, or other suitable containers for shipment or storage. |
Equipment Showcase
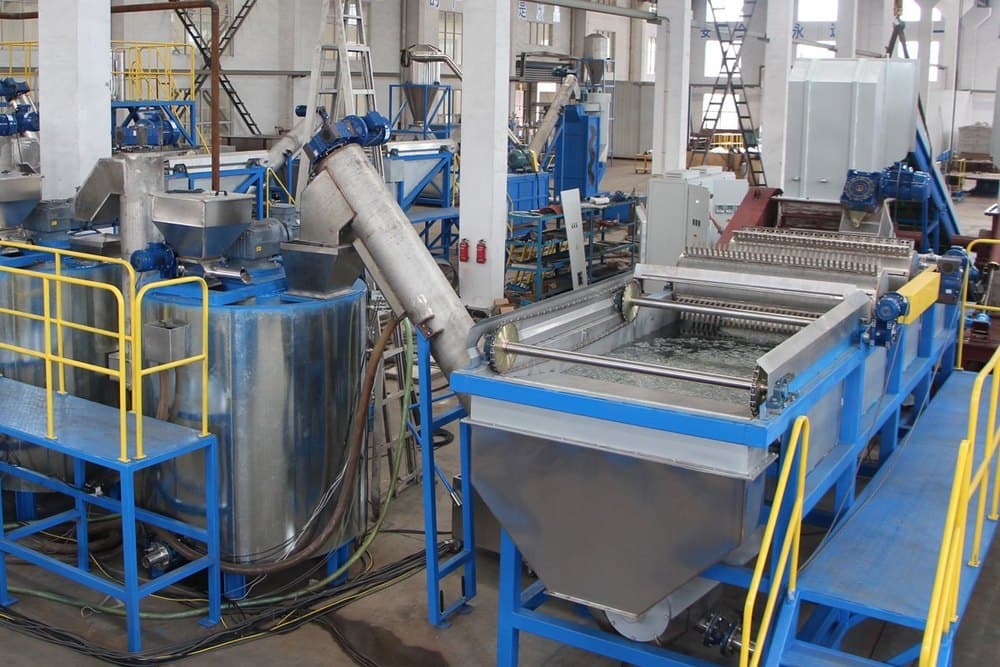
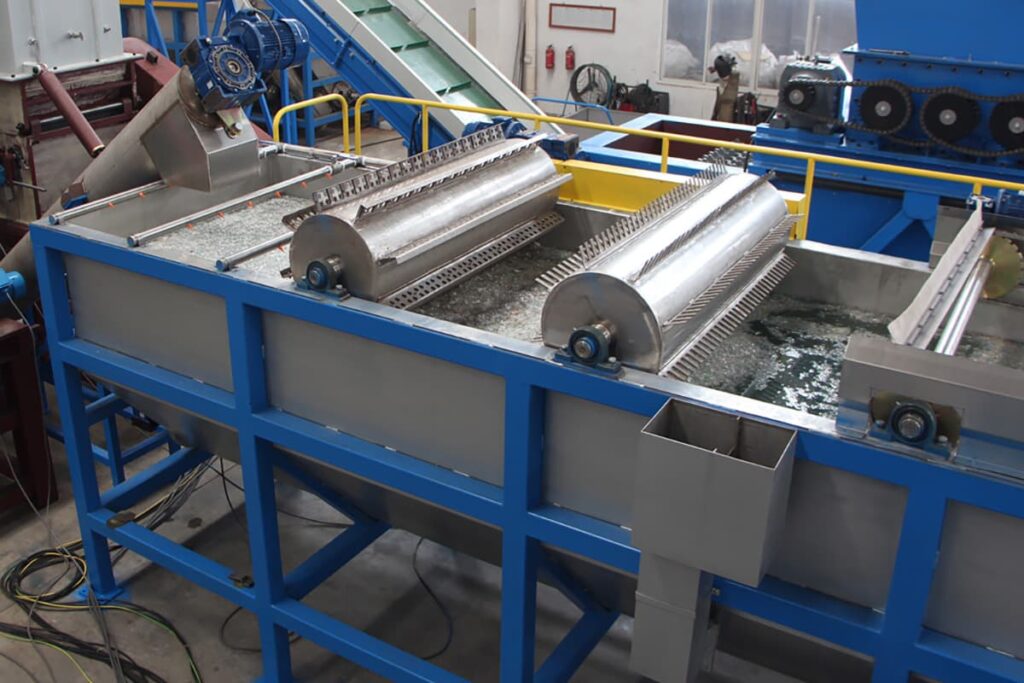

Ready to Transform Your Recycling Business?
To get the latest prices, detailed specifications, and lead times, please send us a message using the form below. Our experts are ready to assist you!
Warranty Information:
All our robust recycling machines come with a comprehensive 1-year limited warranty for your peace of mind.
[…] an affordable yet effective PET recycling line is crucial for small and medium enterprises (SMEs) aiming to balance cost-efficiency and […]